General Motors'(GM) plan of offering an extensive lineup of zero-emissions vehicles by 2035 requires reliable battery sources, and has made a multimillion dollar investment in CTR’s Hell’s Kitchen project, set to begin producing lithium by 2024.
This agreement will supply enough cathode material to produce five million electric vehicles (EVs). Furthermore, it will strengthen North American battery supply chains.
LG Chem
LG Chem’s massive new plant in Tennessee will produce enough NCMA cathode material (nickel, cobalt, manganese and aluminum) to power over one million cars with a range of over 300 miles. GM and LG Chem have taken another significant step toward its plans to become an all-electric company by agreeing on a long-term supply contract for cathode materials that will supply its plans to switch entirely to electric.
LG Chem states its factory will use cutting-edge production technology and begin producing cathode material tailored specifically for North American EVs from day one, expanding capacity and production as market needs change, the company reports.
General Motors has also taken steps to localize its lithium supply chain through several initiatives. Alongside their Tennessee plant, GM recently made an investment commitment to Controlled Thermal Resources’ Hell’s Kitchen lithium project in New York’s Hell’s Kitchen neighborhood – its plan to convert brine deposits into lithium production will enable GM to reduce its dependence on supplies from Argentina, Chile and Bolivia’s “lithium triangle.”
Livent
Part of GM’s new funding will be allocated toward improving their separation technology for electric vehicle (EV) batteries, which should help lower battery cell cost by decreasing lithium-ion cathode active material costs (CAMs). This step is vital if GM hopes to meet its goal of eliminating tailpipe emissions from all new light-duty vehicles by 2035.
LG Chem has agreed to supply over 500,000 tons of nickel, cobalt, manganese and aluminum (CAM) from 2026-2035 as part of a long-term supply agreement that will help GM meet its domestic EV battery capacity plans of 160GWh across four U.S. factory plants by 2025; one being located in Spring Hill Tennessee.
GM is also working with suppliers on the creation of “next-generation” raw materials to reduce costs, such as Microvast’s separator designed to work with all lithium-ion cell architectures and reduce thickness while simultaneously improving cell safety and energy density.
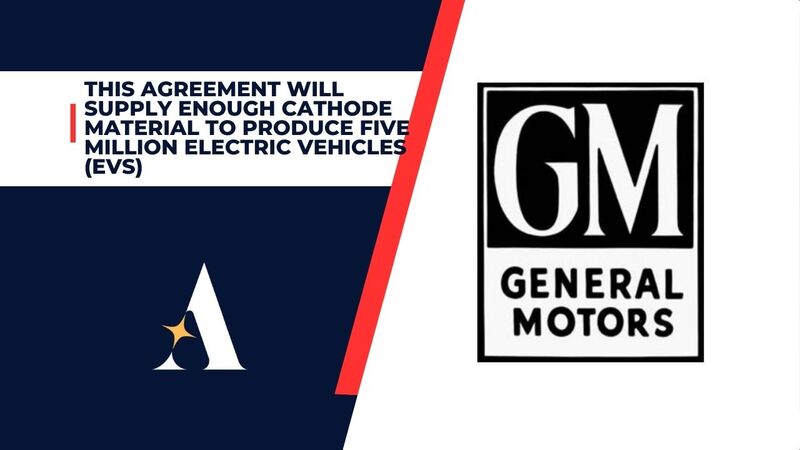
Controlled Thermal Resources
General Motors is making moves to secure supplies amid rising prices for raw materials needed to manufacture electric vehicle batteries, by signing three new raw material supplier agreements totaling more than $1.5 billion in commitments.
LG Chem and General Motors (GM) signed a long-term supply deal that will supply them with nearly 968,000 tons of cathode active material (CAM) between now and 2030 – enough for 5 million electric vehicles (EVs). Processing of this CAM will occur at several GM factories including Spring Hill Tennessee; localizing processing for lithium cobalt nickel manganese aluminum (LCMA) by middecade is also being considered.
GM also invested in Mitra Chemical, a Silicon Valley startup dedicated to battery manufacturing technology. Mitra Chemical’s closed-loop extraction process produces lithium, the key element used in electric vehicle batteries, while producing less tailing waste and carbon emissions than traditional mining pits or evaporation ponds would produce.
Lithium Americas
This deal should supply General Motors (GM) with enough lithium for their plan of building one million electric vehicles annually in North America by 2040 and make its global products and operations carbon neutral.
Similarly, this investment will increase production of cathode active material (CAM) and its precursor materials (pCAM) in North America. CAM is the primary raw material used in electric vehicle batteries and accounts for roughly 40% of their cost; popular examples are nickel-cobalt-manganese alloy and lithium iron phosphate as primary CAMs.
Increased pCAM and CAM processing capacities in the US will also help GM reduce its reliance on Asia, where most current EV battery production takes place. It will also support the company’s initiatives to establish charging stations powered by renewable energy, part of their overall goal to provide zero emission vehicles across all price points by 2035 as well as ensure battery electric vehicles are charged using clean electricity generated from local utility partners.
- Friday Intraday Trading Sees Nvidia’s stock Market Cap Momentarily Cross $2 Trillion
- Trump’s January 6 Civil Cases Proceed While Criminal Case Is Halted
- Trump Delivers Speech at the Columbia Black Conservative Federation Gala
- Trump Declares Strong Support for IVF Following Alabama Supreme Court Decision
- Schumer in Ukraine Declares US Backing During House Aid Standoff